Applications
Friction Welding Holland offers various applications, which we present to you on this page.
Pistonrods
We use our friction welding machine to weld these forged or machined components to piston rods. The result is a fully penetrative weld (surface weld). Both components are forged into one piece.
We can process diameters ranging between approximately 20 mm and 90 mm.
Besides friction welding, we provide added services by performing pre- or post-machining on one of our CNC controlled lathes. This enables us to supply a complete product from start to finish if required.
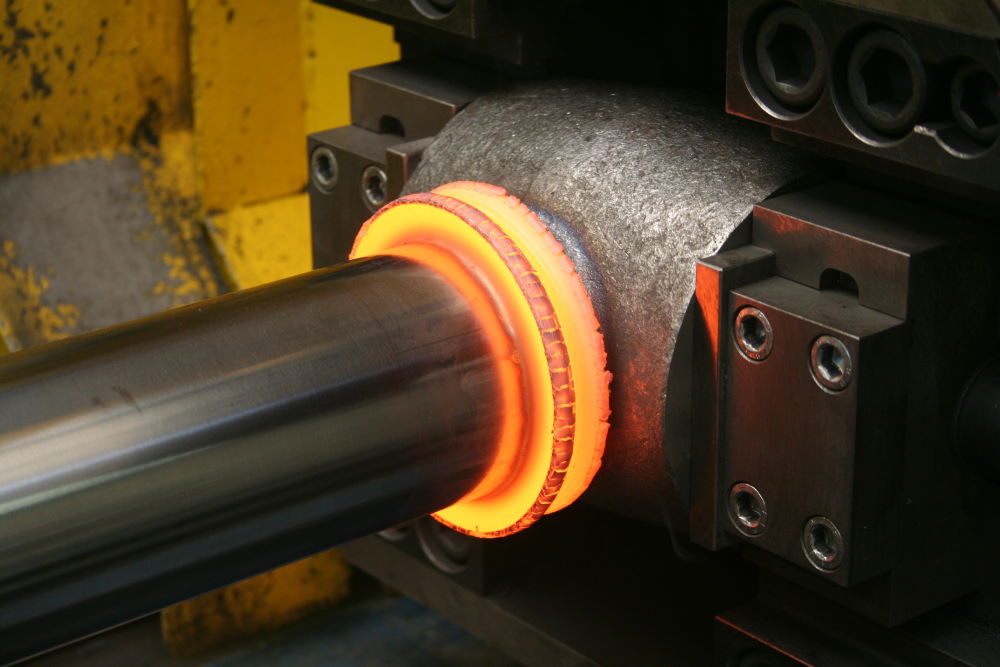
Cylindertubes
We weld cylinder tubes for hydraulic cylinders.
Materials that can be welded as part of this application include St52, St37, etc. It’s often necessary for forged or machined components to be welded to these tubes. We use our friction welding machine to weld these forged or machined components to cylinder tubes. The result is a fully penetrative weld (surface weld). Both components are forged into one piece. We can process diameters ranging between approximately 20 mm and 160 mm.
Besides friction welding, we provide added services by performing pre- or post-machining on one of our CNC controlled lathes. This enables us to supply a complete product from start to finish if required.
Drive shaft
Also for drive shafts you can contact us.
Drillpipes
Drillpipes are also perfect for a friction weld. Because of the high torque what will be achieved our customers choose for this kind of weld.
Saving materials
If you want to save money on the purchase of material we can weld a bigger piece of material to a smaller shaft. So you don’t have to machine it down completely.
Long-term savings for machinists!
If a large amount of a certain material must be lathed/machined (e.g. for an axle housing), you might consider having it friction welded instead. A simple example involves the welding of a rod to a flange (as part of the manufacture of an axle housing). When such a product is machined from a large block of steel, a lot of material mass and machining time goes to waste.
Friction welding, on the other hand, is a fast and efficient process that creates joints as strong as the steel itself. The greater the mass to be processed, the more machinists can save in cost price and engineering time by having us friction weld their products. The diagram illustrates this.
When compared to current welding techniques, friction welding is also sustainable. Friction welding is a sustainable method and the burden placed on the environment during the production process is significantly lower than traditional welding techniques.